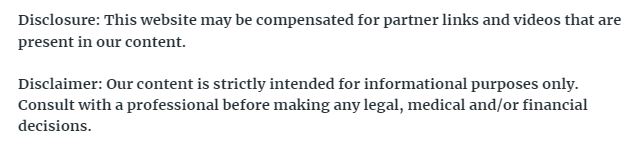
Manufacturing today involves many steps, from pouring molten steel to welding to installing wires, cables, hoses, or burnishing metals. Getting all this work done means using the right tools and machinery for the job, and many products made in the US such as Burr King and other brands have the right tool to make a quality finished product. A metal tumbler machine or a commercial rock tumbler, for example, may be similar to burnishing and help modify a metal’s surface to gain a new aesthetic (although this work will not actually remove scratches, one should note). Burr King and other brands can use extreme tumblers, vibratory finishing equipment, and more to ensure that any finished metal product is free of imperfections. How can this be done?
What Burr King and Others Do
What is the work of Burr King and related brands? They will take care of the metal imperfections, or the burrs, that naturally appear on semi-finished metal products. Sharp raised ridges and imperfections on metal would be unacceptable to customers, so brands such as Burr King and others will use a rectangle vibratory tank or other equipment to mechanically grind off such imperfections and create a smooth surface for a finished metal product. Vibratory finishing, as a whole, involves four elements to get the job done: parts, media, compound solutions, and equipment. These liquids used as finishing materials may vary in pH from 1 to 14, and 4-14 stands as the most popular range for this. And when choosing the right media for a vibratory machine, any worker is advised to choose a media that is 70% of the size of any hole in the machine for maximum output.
What kind of burrs and other imperfections might present themselves? In drilled holes, for example, can interfere with fastener and other materials, so brands such as Burr King will remove them. Burrs on drill holes may also cause undue stress on the edges of holes, and even decrease resistance to fracturing and shortening the fatigue life. Not to mention how a fastener might come loose if it is secured to a hole that still has its burrs in place.
Burrs may cause other problems, too. They can attract electrical charges that may build up and then interfere with electrical components, and these burrs might also cause excessive heat or friction in moving parts, not to mention how uneven metal surfaces may be vulnerable to corrosion due to their uneven thickness and surfaces.
Manual deburring was often done in the past with tools such as sandpaper, scrapers, files, and even stones, and today, for a more consistent deburring job, brands like Burr King and others can use machines that will smoothly remove burrs from finished metal products and ensure even, tempered surfaces that are ideal for the finished product’s intended use. In fact, even thermal deburring may be done, which is when an explosive gas mixture is set off to remove burrs with sheer heat. For safety, this work is done inside an explosion-proof chamber on the work site. This process is very fast, lasting for only about 20 milliseconds, but it can get very hot: a peak temperature of 5,430 degrees Fahrenheit (3,000 degrees Celsius) can be expected from this process.