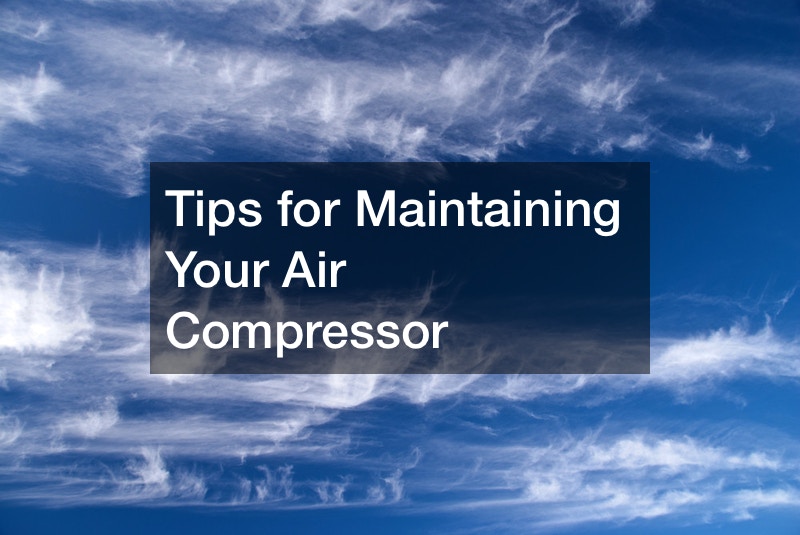
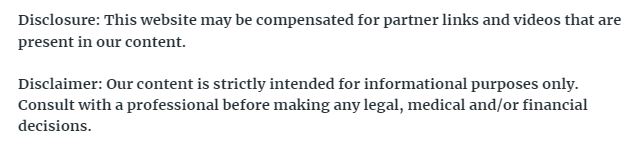
Purchasing a new air compressor can be expensive, especially if you are working on a tight budget. You may have experienced a failure in the air compressor unit, making you slow down business operations. A used air compressor does a good job and will cost you less. It provides a temporary solution for operations that need air compressor technology to run.
Air compressors have durable machinery that gives the equipment a long lifespan. If the previous auto tire air compressor owner maintained the equipment effectively, you are assured that it will not fail within a few months. The lifespan of a rotary air compressor is more than a decade, and a reciprocating one can last up to three decades.
Buying an air compressor from a reputable dealer provides you with an updated record of the machine’s history and usage. You can find out if the equipment was regularly maintained and if there are wear and tear issues. The record helps you to make an informed decision when making a purchase. Used air compressors allow you to experiment with the functionality and effectiveness of the machinery.
There are various uses of air compressors, such as running heating and cooling systems and power tools. You can search for an 8 gallon air compressor for sale to meet the needs of your business.
If your job relies on an air compressor, it is important to keep that air compressor safe and working well. Otherwise, you might not be able to do your work and your business might suffer. From the start, you should buy the most reliable air compressor you can afford. An air compressor unit might cost more than another one based on its quality or brand. So it is important to research your options before purchasing. You should also know the air compressor basics when you buy one. Make sure you’re running your machine correctly and know how to do basic maintenance on it. When you can afford them, buy air compressor accessories that can help you take care of your machine and extend its life. And finally, know when to bring in an air compressor specialist to take care of it. No matter how secure you are with the compressor, there are going to be things you don’t know how to do. If you bring in a professional instead of trying to take care of it yourself, you’ll keep from making big mistakes.
Many businesses use air compressors to do their daily activities whether it is on a construction site, cleaning, or building items. These machines need to be properly maintained to be able to work properly as they are a large investment and a huge part of people’s ability to do their jobs. Here are a few things about the proper care and maintenance of an air compressor.
Take the time to study your compressor’s manual so you know everything there is to know about the machine. Every machine is built a bit differently so the more you know the less surprised you will be if you run into a problem. Many manuals have maintenance tips and tricks as well to keep your machine in its best shape. Another great reason to read the manual is to ensure your warranty stays valid. If you don’t follow the guidelines within the manual your warranty may be void and you will have to pay out of pocket to fix it or buy a new one. The manual will tell you what types of oils, hoses and connectors your machine requires and inform you of the proper fluid metrics to follow.

Ensure you drain the machine properly of any moisture or air that is trapped within. Depending on what type of machine you have there should be a plug to drain moisture from the tanks. If you live in a humid climate you may need to drain more often.

Always make sure your intake is clean and working properly. Your machine will have to work twice as hard if your intake is clogged or dirty causing power problems and eventually burning out the engine. If you work around a lot of dirt and dust be sure to check the valves regularly. When checking your intake take the time to clean all air filters as they tend to build up with dust and dirt.
Air compressors vibrate a lot when they are running. This can loosen nuts, bolts, fasteners, and other pieces so always check them to ensure they are tight and in position.
The hoses on a compressor are one of the most important components to keep the machine performing at its best. Check your hoses for any signs of damage, cracks, or excessive wear as this could lead to leaks and unnecessary strain on your machine. Regular reliability-centered maintenance of all working parts will ensure your machine stays working so you can keep working too.
Doing regular oil changes can ensure your machine is running smoothly for hours at a time. Changing your oil every 500-1000 hours of use is the best way to stick to a schedule. During a synthetic compressor oil change, as much as 20% of the old acidic fluid is left behind and will contaminate and reduce the life of the new oil. Be sure to check your manual to be sure you are using the correct fluid metrics. Compressor oil analysis studies have shown the importance of flushing your system and correctly maintaining fluid metrics.