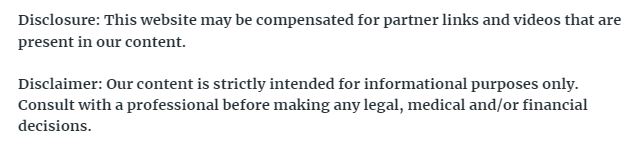
It’s the little things that count. Doesn’t matter the industry or even your personal perspective on life. It’s just the way it is!
When you’re looking over your bellows you’ll realize this all over again, particularly if you’ve been feeling the hurt over struggling equipment. When your exhaust flex pipe shows some strain, the only thing to do is seek out a replacement. Which one, though, takes a little more research. You don’t want to just swap out your equipment with something worse. Learning how metal bellows are made and the work that goes into the bellows expansion joint will ensure you’re never left wondering what could be better.
Check out this quick rundown to both save you money and improve the performance of your bellow forming machine.
Know Your Melting Points
Missing out on this detail is an accident just waiting to happen. Every metal has its own unique melting point and should be carefully measured no matter the application. Iron ore often melts at 2,750 degrees Fahrenheit, while steel follows close behind with a melting point of around 2,500. Metal expansion joints are usually made with these high temperatures in mind, but it never hurts to be careful. You can always run into shoddy metal mixtures that end up doing more harm than good.
Check Out Your Metals
Speaking of which…how familiar are you with your different types of metals? As touched on above, iron ore and various kinds of steel are commonly used when creating single expansion joints. Back in 2015 researchers at Brown University discovered a new material with the highest melting point of any substance at 7,450 degrees Fahrenheit. It’s composed of nitrogen, carbon, and hafnium, to date one of the most impressive metal constructions yet seen. Think how much longer your metal bellows could last with a simple switch.
Pay Attention To Environments
The environment in which your bellows expansion joint is exposed to will go a long way in determining its durability. Take the ocean and salty air, for example. To better resist the corrosive effects of salt in marine environments Marine Grade Stainless Steel was designed to contain a healthy amount of molybdenum. This element has the atomic symbol of 42 and a melting point of nearly 4,800 degrees Fahrenheit. Stainless exhaust flex joints take a lot of work, sure, but it’s worth keeping your equipment from breaking down prematurely.
Never Forget Regular Applications
How often are your multi-ply bellows used? What are they used for? These questions will make sure you’re not wasting your money or your time. Hastelloy X is widely considered to be a fantastic metal, well-suited to high temperature applications without so much as a dip in quality. This extreme temperature alloy is commonly used in aerospace, though it is affordable enough to use in commercial metal bellows. Think 1,600 degrees Fahrenheit, on average.
Replace Joints As Soon As Possible
Think your bellows expansion joint doesn’t have much longer to go? Swap it out at the nearest sign. Multi-ply bellows consist of two to three tubes, usually, though they have the capacity to have as many as five tubes depending on the application. A more custom bellows design usually requires focus on attributes relating to stress modes, flexing, and pressure differences. Expect to get used to exposure and vibration when it comes to maintaining longevity, too.
Feeling a little more confident? Embrace the little things and make sure you buy the perfect bellows expansion joint next time you’re noticing an issue.