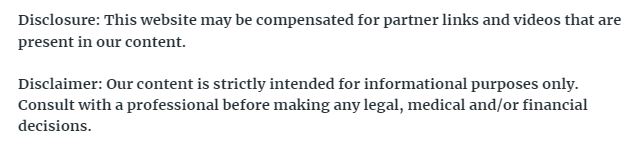

Plastic bottles are a big part of our lives, although we often don?t take note of them. Since approximately 1500 plastic bottles are consumed every second in the US, or 2.5 million every hour, it might be useful to know how they are made and how blow molding works.
Blow molding is a technique for making hollow, one-piece plastic parts with thin walls, such as gallon plastic jugs, plastic storage jars, and similar plastic containers. Depending on the product, different materials may be used, such as polycarbonate thermoplastic elastomers, K-resin, and
polyethylene. Drink bottles are commonly made from polyethylene terephthalate (PET), because it is lightweight and strong.
The blow molding process begins with a tube of hot plastic in a cylinder, called a parison; after which the bottom halves are connected. Using air pressure, the plastic then expands to fill the shape of the cavity., and, after the shape has cooled, the mold opens and the new container is ready. Most custom bottle manufacturing blow machines have three main parts: the extruder, accumulator die, and the molds themselves.
With various kinds of bottles and plastic containers, it makes sense that the manufacture of plastic bottles would have a few variations on how blow molding works. Currently, manufacturing companies can select either extrusion blow molding, injection blow molding or stretch blow molding as specific methods. Extrusion and intrusion blow molding, for instance, have end products that are suitable for different uses.
Extrusion blow molding is an automated production operation that is often combined with other operations, such as bottle filling and labeling. It?s made, as its name suggests, in a slightly different sequence. Injection blow molding, by comparison, starts with the parison being injection molded. It has a lower production rate and is not as commonly used as extrusion methods. However, because PET is so strong and works best with stretch blow molding, this method is a good choice for bottling carbonated beverages.
Rotational molding, another technique for creating industrial plastic containers, uses the force of gravity within a rotating mold to create a hollow form. It is especially useful for thermoplastic polymers, but other uses are in development for elastomers and thermosets. For the most part, rotational molding, also known as rotomolding, is used for larger parts in lower quantities, as opposed to the millions of bottles and parts produced by extrusion methods.
Another important aspect of how blow molding works is in regards to recycling, reusing materials, and saving energy. For example, leftover materials and trimmings can be reused after they are remixed with some unused material. According to the National Association for PET Container Resources (NAPCOR), over 5 million pounds of PET bottles and jars were available for recycling in 2013. In addition to recyclability, the technology for blow molding is increasingly advanced and, with its adaptability to automated manufacturing and high level of productivity, plastic blow molding companies can save energy and production costs.
Aside from millions of plastic bottles, how blow molding works can be applied to many other products, such as pharmaceutical bottles, antifreeze and insecticide containers, one piece plastic items like lawn chairs, garbage cans, and even fuel tanks. How blow molding works will continue to change and improve as technology advances, and as new uses for plastic are developed.