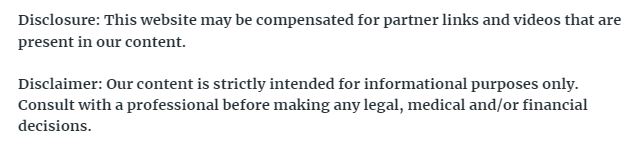
To say that manufacturing is an important part of the United States economy is an understatement. Every year, American manufacturers contribute billions of dollars to the U.S. economy and manufacturing accounts for a large part of the American workforce with more than 10 million people working in the manufacturing sector.
With such a high rate of manufacturing, it is important for companies to be able to produce goods and services in a timely manner. One may to make that happen is through the use of lean manufacturing? What is lean manufacturing you ask? It’s a series of methods that help minimize material waste while maximizing labor to increase production levels. Ultimately, lean manufacturing is all about improving total productivity, which means making all parts of the process efficient.
Lean manufacturing is a popular system in Japan where inventory levels are kept low and automation processes are supervised by humans to ensure better quality control. Ultimately, lean manufacturing aims to maximize manufacturing by giving a customer a quality product in a timely manner.
Benefits of lean manufacturing include:
- Better quality: With improved efficiency, employees free up time and resources for improving quality control standards in a company’s manufacturing processes.
- Sustainability: By cutting down on waste and being able to adapt, a company puts itself in a good position to be better equipped to handle future production and business.
- Happier employees: Without efficiency, workers are forced to work with packed schedule with many different tasks. Having to come to work knowing you’ve got a packed schedule can leave you low on morale. Fortunately, lean manufacturing can boost employee morale by boosting productivity.
- Better lead times: As lean manufacturing helps streamline different processes, businesses are able to adapt to changes in demand and other changes in the market. This results in fewer delays and better lead times.
Lead time is the period between the start and end of a process i.e. the time between the placement of an order for a product or a service and the finish and delivery of that product or service.
Companies can shorten lead times in many ways, whether it is through automation, improving logistics or nearshoring. Short lead times mean that goods are produced faster and ultimately consumers get those goods quicker. - More profits: Lean manufacturing will increase efficiency and streamline operations, which should increase profit for your company.
Now that it’s been established what lean manufacturing is, let’s take a look at different types of lean manufacturing in practice:
- Employee training: Companies can maximize their potential with a lean manufacturing system by training employees on the ins-and-outs of lean methods and how those processes are used in production.
- Inventory reduction: The use of lean manufacturing processes usually leads to inventory reduction and regulation. This is often done using a Kanban system. With a Kanban system, an employee takes a card to a supervisor and only then does that supervisor replace or procure inventory. This helps companies avoid having a surplus of materials that they don’t use.
- Better production: One of the keys to lean manufacturing is an assembly-line sort of model when it comes to production. Automation helps increase production and human workers work in conjunction with machines to help maintain quality control.
- Process mapping and value stream: These two things involve charting and evaluating specific production processes to better understand the whole operation. This helps identify areas of waste and pinpoint issues which can either be addressed or eliminated. In short, by mapping out production, companies can identify ways to optimize production.
Manufacturing gives a positive boost to the US economy and its workforce. While there are many complex operations involved in manufacturing, three basic operations include milling, drilling and turning. The successful implementation of these operations allows companies to manufacture goods consistently and can lead to short lead times if companies embrace ways to improve their manufacturing processes and their logistics.
Manufacturing consulting firms can help your company find ways to maximize production. There are more than 700,000 consulting firms worldwide and a consulting firm can help you optimize your facility design and help improve your process design and layout.