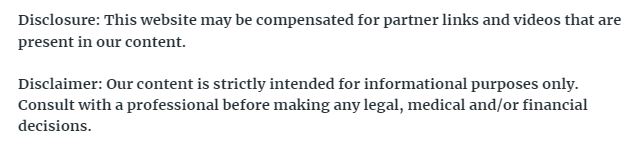
It’s A Handy Reference Tool For Metal Surface Finish Characteristics
A surface finish chart is a reference material we at Metal Cutting sometimes use internally as part of our quality assurance process. (You can read more about our quality measures on the Quality Commitment page of our website.) Typically, such charts provide guidelines regarding the measurement of surface finish, such as the parameters used, the typical roughness according to different processing methods, or the conversion from a unit such as stainless steel to microns (or micrometers, µm). Such as astm a666.
Surface finish is generally described as a measure of the texture of a surface, characterized by the lay (or direction) of the surface pattern, its roughness, and its waviness. What exactly will you find if you search the web for a “surface finish chart” and how does it relate to metal surface finish? What is astm a666?
Units Of Surface Finish Measurement
One type of chart shows the surface finish parameters — that is, the different units of measurement and arithmetic calculations that are used to describe surface finish. Generally, this chart would include the commonly used Roughness Average, Ra, which is a calculation of the average length between all the peaks and valleys (or the average height) from the mean line of the surface. Because it neutralizes any significantly outlying points, Ra is not sensitive to occasional spikes and gouges.
The Root Mean Square Roughness, or RMS, is similar to Ra but generally considered to be an approximation and therefore, less accurate than Ra. RMS is calculated using an algorithm that finds the square root of the average of the squares of the values; basically, RMS turns the surface profile in to a sine wave and measures the average deviation of the curve from the mean line.
Maximum Roughness Depth, Rmax, measures the vertical distance from the highest peak to the lowest valley within five sampling lengths and selects the largest of the five values. This is a very sensitive method of estimating surface finish and is vulnerable to burrs or scratches that lead to a higher reading, indicating a rougher surface. The Mean Roughness, Rz, astm a666 is calculated by averaging the height of the five highest peaks and the depths of the five lowest valleys. Because it looks only at the extremes only, Rz produces values that tend to be high and may not be an accurate reflection of the average surface finish.
At Metal Cutting, we typically test for Ra, and it is what most of our customers ask for. Although Ra and RMS are sometimes used interchangeably because the conversion factor is RMS = Ra x 1.1, we encourage customers to use Ra, which is considered more accurate and is widely accepted in the industry.
Feasible Roughness For Different Processes
Another type of surface finish chart shows the average range of surface finish values that can be achieved using different types of manufacturing processes. This is important to know because surface finishes can vary greatly depending on the process used to produce them; this is also why deciding between different cutting methods is an important step if having a particular surface on your finished metal parts is critical to the success of your application. In addition, achieving a particular surface finish may require that more than one process be used.
Each metal cutting process has its own characteristics (what machinists call “witness marks”), which can be varied to a certain degree and with certain limitations, also depending on the process. Where there is a floor on how smooth a machined surface can be, polishing can be deployed to achieve a highly smooth surface or grinding can be used to create a sharp edge or shiny finish. Therefore, you can look for a surface finish chart that lists the relative surface finish roughness for various metal cutting methods, such as abrasive cutting, EDM, astm a666, grinding, milling, turning, lapping, polishing, and so on.
Before you look into metal sales near me for thin sheet metal and copper brass, make sure you do all of your research first.