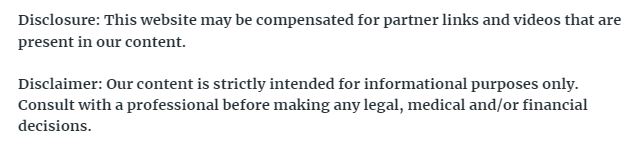

Humans and insects may have both developed techniques for boring holes, but humans have the advantage of boring tools and using a boring head with a high level of precision. When researching boring heads and techniques there are several criteria to look at.
Boring mills can consist of vertical boring mills or horizontal boring mills. In a vertical mill, the workpiece moves or rotates around a vertical axis and the boring head moves in a linear fashion. The workpiece sits on a table and the boring bar rotates on a horizontal axis in horizontal boring mills. Size and application will determine which setup makes the most sense for your situation.
The final surface finish from using a boring head is typically from 32 to 125 microinches, but can range from 8 to 250 microinches. Different boring inserts can determine how effectively you get to the final finish or roughness, or if you need additional internal cylindrical grinding. Your final geometry from lathe boring can result in straight holes or tapered holes from your boring head.
Regardless of your boring head needs, a proper boring setup and technique can reduce additional production costs along the way. The high level of precision could mean an advantage to using appropriate boring heads in manufacturing. Reference links: parlec.com