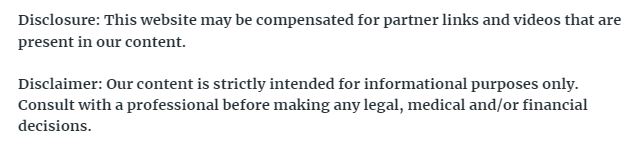
Polyurethane is one of the most malleable materials on the market. Not only can it be applied multiple times without concern of wear, it’s capable of resisting high heat, electricity, and extreme weather.
The polyurethane molding process can take many different forms, though these are the most common ones utilized in the industry.
Open Cast Molded Polyurethane
One of the most easy and basic methods, it’s usually employed with the design doesn’t involve any intricate details. However, it is extremely durable and highly cost effective.
Compression Molding
This process involves placing the liquid polyurethane into a mold. The mold is then run through a compressor that applies high levels of heat. Using this method allows for a higher level of detail, though it tends to be more extensive than open cast molding.
Centrifugal Molding
This process of molding uses high speed rotation to solidify the polyurethane. After being placed into a mold, the casing it placed into a centrifuge. The spinning causes the material to harden as it sets against the mold. This method is good for smaller components and pieces, but is unsuitable for larger parts.
Foaming
With this process polyurethane is left to set in molds, and harden over time. The foaming method takes longer than the previous methods, but results in an extremely durable product.
Polyurethane Injection Molding
The polyurethane injection molding process uses high speed to shoot the material into a mold. With injection molding the polyurethane can either be liquid or small hardened droplets. Using this method you can achieve a wide variety of results which makes it one of the most popular in the industry. The polyurethane injection molding process is also easy to automate, and relatively low cost. Additionally, any waste material can easily be consolidated back into the system for use in future molding. The main drawback with this type is that the products tend to be less resistant to extreme heat and pressure, making the product more easily compromised over time.
Encapsulation Molding
This method of molding helps strengthen the final product by placing inserts within the mold. Using this method you can create durable products capable of withstanding larger amounts of stress.
Polyurethane molding comes in may forms, and the method used depends on the piece you’re trying to make. There are pros and cons to each process; the polyurethane injection molding process being best for quick automation and easy results across a spectrum of components. The foaming method on the other hand creates pieces that can withstand more abuse over longer periods of time.
Depending on the polyurethane product you’re looking for, it’s worth looking into the process used to make it so that you know what to expect in terms of its durability. You may also be able to request custom made pieces if you’re unable to find exactly what you’re looking for.