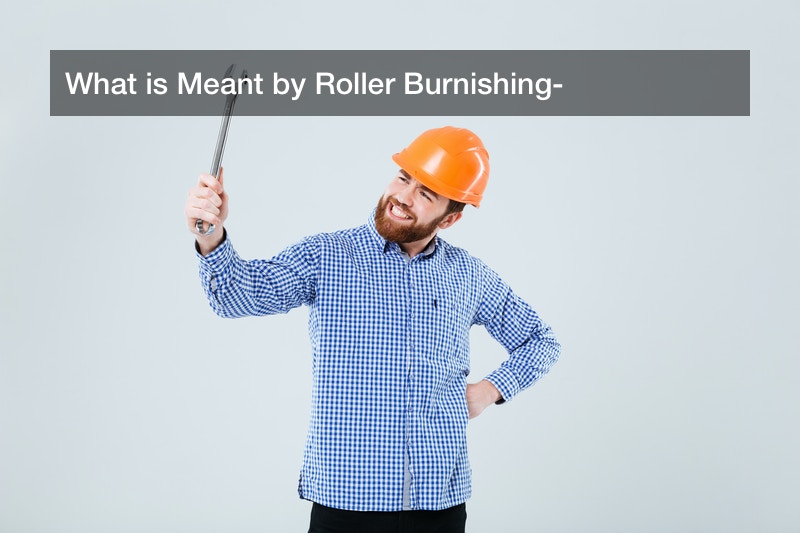
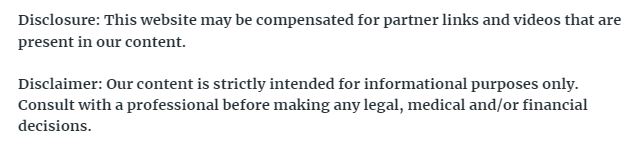
Finishing a metal part to achieve a mirror-like surface has evolved over time to include even more sophisticated methods of burnishing. However, there are simpler methods such as roller burnishing where you can achieve a smooth surface for your metal part without removing any part from it. In simple terms, burnishing can be described as the process of polishing surfaces such as metal by sliding the surface through a harder object. This process eliminates the more complex techniques of burnishing that will require you to check the feed rates and dimensional accuracy in order to achieve precision metal finishing. There are different approaches to burnishing surfaces depending on the type of surface and the tools being used. This means that a process involving diamond burnishing will require specific burnishing tools compared to how you would carry out a similar process on a different surface.
Different Approaches in Burnishing
When you are machining a surface such as a metallic surface, there are microscopic valleys and peaks that are left on the surface called roughness unless you are using the chipless machining method. Regardless of the surface, different burnishing tools will produce a varied finish considering that burnishing is all about reducing the roughness. Machining tools take into considerate the feed rates that determine how smooth the surface will be. With the perfect feed rate, a burnished part will appear as if a metallic surface has been smeared smooth. In roller burnishing however, the concept of maintaining the feed rate does not apply as the burnishing tool’s rollers perform what is known as cold flowing on the surface and the sub-surface of the metallic part.
Which Parts Work for Roller Burnishing?
A common question in manufacturing is about how to use a burnishing tool but the aspect of which parts actually work for roller burnishing hardly crops up. There are a few things you need to understand about roller burnishing apart from the feed rate. The process of roller burnishing is repetitive and fast. However, not every part can be burnished using this method. For the best roller burnishing results, the metals in use have to be ductile or malleable. This is despite that almost every metal can be roller burnished. The best examples of metals that can be roller burnished include; stainless steel, iron, aluminum, copper, bronze and brass. Another important characteristic of the metals being roller burnished is that they should have a hardness of less than 40 HRC. This quality does not eliminate materials that have a higher hardness. Hardness mainly affects the feed rates which is why metals with a hardness of higher than 45 HRC cannot be effectively burnished using the roller method.