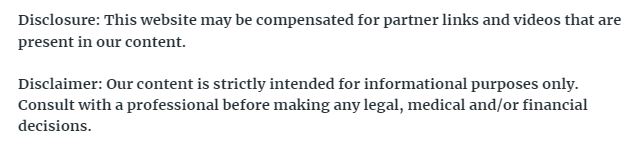
Furnaces are used throughout a variety of professions because of its ability to produce extremely high temperatures for steel melting. The prevalence of furnaces has gradually increased in prior years due to the introduction of different methods by using electricity from an electric arc furnace or an induction heating through induction furnaces. Furnaces are a great resource to business, mainly because of the sturdy material it’s creating from—steel.
The Differences In How Heating Furnaces Are Manufactured
There are varying rules and regulations in each country that ultimately determine how things are produced and its overall quality in comparison — however, they all one thing in common—steel. Steel is referenced as one of the world’s most important and abundant resources, nearly 13% of the world’s steel is used in the automotive industry, and half of the world’s steel is used for buildings and other infrastructure that. The differences lie in how steel is used to create furnaces—particularly, in Canada, there is immense pride taken into how furnaces are designed, down to service and parts to ensure they’re producing a quality product that businesses can rely on to fuel them on a day-to-day basis. In fact, approximately 17% of U.S imported steel comes from Canada. Canadian made furnaces take various factors into account before manufacturing a product because there is an emphasis placed on the importance of encompassing all factors that most companies and consumers would look for when purchasing a furnace, like a guarantee for energy-efficient regardless of any type of furnace chosen.
What Are The Leading Canadian Induction Furnace Manufacturers?
AMLET: These manufacturers are well-educated and experienced with induction furnaces and melting furnaces. More specifically, they focus custom designing aluminum and steel melting induction furnaces to allow the functions of a melting furnace to be versatile and equip to meet different businesses’ needs. Their products are rated as top-tier because of their dedication to details in functionality, which includes using the latest advancements in technology to create furnaces that are exceptional.
Inductotherm: The top-tier leading induction furnace company in Canada and the world. Inductotherm Corporation designs their melting and heating systems through using various naturally occurring metals in the Earth. The methods used to develop an inductrotherm melting furnace offers a level of quality and technology intertwined that is beyond the standard. Furnaces are designed with both functionality and uniqueness in mind to create a truly different experience in every Inductotherm furnace—metal is considered the standard foundation material, but this company defies those boundaries by introducing a gold melting furnace and copper melting furnace that provides an undeniable edge in new-age furnaces. Designs similar to their gold melting furnace are gray and ductile iron, steel, copper, and copper-based alloys, zinc, silicon, graphite heating, and other reactive and precious metals that undergo induction melting and induction hardening.
What’s The Difference Between Non-Steel Melting?
1. Aluminum Melting: The process consists of introducing an induction heating coil that converts pure aluminum into aluminum alloys that undergo an energy-intensive process to create the changes — energy-efficient furnaces built by Inductotherm that are second to none.
2.Cooper/Copper Alloy Melting: These furnaces are built from melted pounds copper and brass for custom casting to create a piece advanced induction technology that combines copper and copper-based alloy to yield a furnace that is a temper-controlled and minimal gas pickup with relatively low metal loss and an eco-friendly process.
Iron Melting: Nearly all metal tonnage is comprised of iron, which makes it an efficient and dependable metal that produces the most quality equipment on the market along with an affordable price tag that makes it even more desirable to buyers. Iron is available for all steel melting operations—induction hardening, heating, holding and pouring.
Precious Metals Melting: Comprised of some of the most quality metals found of Earth, Inductotherm manufactures takes it a considerable notch up by using a selective process for only precious and platinum group metals for all components, spare parts, replacement parts, and even some refurbished equipment. Their method allows increased metal recovery and lower processing cost that makes it one of the most efficient and cost-effective means of acquiring a gold melting furnace.
Rare Earth and Other Metals: Similar to the process of precious melting’s operation, this method extracts those methods towards this set of metals to create a sturdy, efficient furnace.