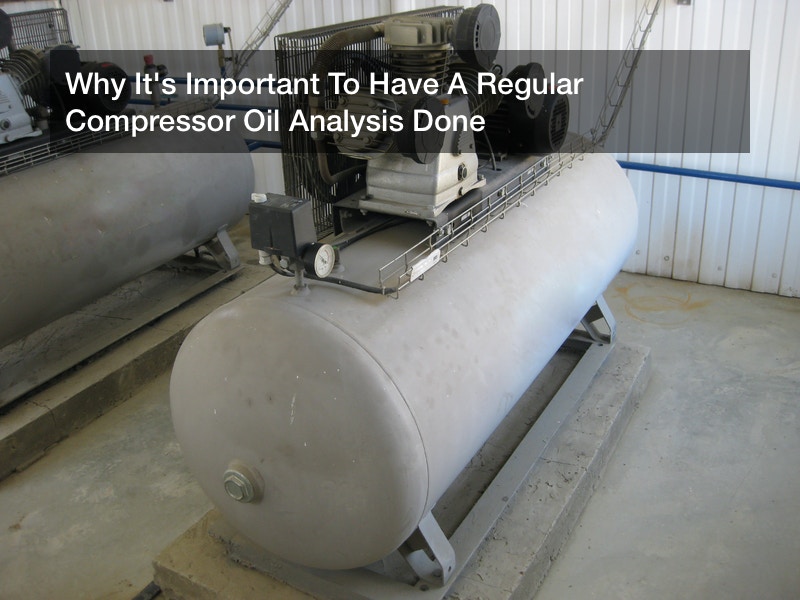
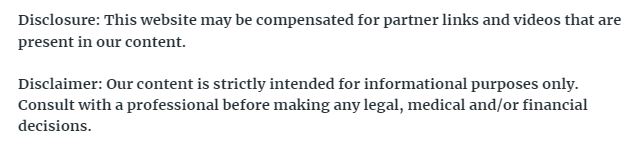
When it comes to manufacturing, nothing can shut up relations down faster than a compressor that’s on the fritz. To make sure that doesn’t happen, it’s imperative for manufacturers to manage compressor lubricants regularly.
Within compressors, lubricant fluid has multiple functions to keep a compressor running as it should. It lubricates the moving parts. It helps seal the compressor off from leaks and can even help manage temperature during operation. Compressors can actually run for many many years after being filled with a specified lubricant, but any contamination requires immediate action.
If you feel your company’s compressor is not functioning as it should, it’s best to reach out to a company that can do a compressor oil analysis for you. Within the compressor oil analysis, a company will check your compressor oil for oil health, viscosity, water and other contaminants which may be causing it to malfunction. It’s absolutely imperative for companies to monitor contamination, particularly from acids and ultra fine solids. Acids are the top reason that compressor fluids fail in need to be replaced. Problems search as oxidation, ingestion from the atmosphere and residual contamination from a previous oil fill are the three main sources of acids found within a compressor fluid.
Let’s take a closer look at some of the categories involved in a compressor oil analysis:
- Oxidation: Oil foams expose compressor fluid to air which causes oxidation and lowers viscosity.
- Viscosity: managing oil viscosity is absolutely important when it comes to compressor help. During the manufacturing process, lubricants come in contact with a lot of different elements, that can affect the viscosity of the fluid. Over time this can impair the fluids ability to cool your compressor unit and probably lubricate all the moving parts that are involved in your manufacturing processes. A viscosity increase within 10% of the new oil viscosity is typically considered normal.
- Bubbles: As foaming oil churns in the compressor, bubbles form and cause the viscosity to drop.
- Dilution: This results from compressor fluid coming into contact with gas, which can also lower the viscosity.
By undergoing a compressor oil analysis at least once a month, your company will be able to keep up the overall health of its compressor, eliminate the chance of unexpected failures and be able to keep your manufacturing processes functioning like clockwork. You’ll want to check all your air compressor parts, especially your compressor oil purifier so as not to cause any conflicts with your compressor warranty.