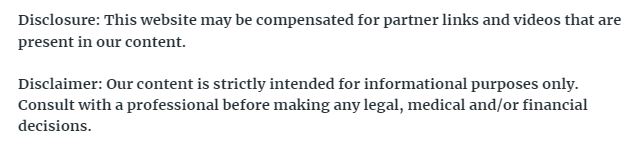
Screws are the foundations of nearly everything around us, the importance of screws is beneficial to upholding the fabric of our society. The structural advancements of we’ve made allows for amazing architectural feats to be made that include numerous buildings that are known for their unique designs. The toughest jobs require the strongest screws, and there’s no shortage on the number of projects in progress— the screw, nut, and blot industry employed 131, 949 in the U.S alone and reached $30 billion in revenue in 2017. Though, as we progress, there’s a tendency to forget how imperative even the smallest materials are to creating the world we see today. The ability to simply ignore or forget what we’ve come from leads us to take for granted the vast achievements made in such a relatively short period. The concept of screws finds its origins in approximately 200 B.C, when screws were handmade—no two where ever alike, making them one of the earliest known versions of a custom screw.
What’re the Differences In Custom Screws?
1. Plastite: This screw offers an easier drive than other screws on the market. Its three lobes are equipped with full relief of the thread form to reduce the driving effort and significant operator fatigue. The additional holding power is also a practical advantage among the custom screw options available; its design allows the custom screw to take advantage of its cold flow materials to establish a resistance to vibration loosening. The deep, coarse spaces threads provide a much heavier sheer area and deeper thread engagement that betters its holding capabilities.
2. PT Screws:The design of a PT screw is created with innovation in mind to provide quality service to consumers looking for a durable, dependable custom screw that’s multifunctional. The most recent PT screw, the Delta PT places advancement at its forefront, apparent in its design. The features are comprised of a compound geometric flank angle of the thread that benefits the deformation and fastening process with increased service life. Unlike the other versions of the PT screw, Delta PT guarantees up to 50% of improved torsional and tensile strength that optimizes pitch and provides a higher clamp load with low contact pressure.
3. Hi-Low Screws:The concept of Hi-Low screws were designed with detailed projects in mind—commonly known as being a screw that varies in many sizes, from small to tiny screws they offer a selection that can be widely used for many projects. This custom screw is equipped with a reduced minor diameter and a double lead high with a low thread that minimizes the possibility of material displacement. Its well-crafted design makes for providing positive thread engagement that requires a performed hole for proper use.
What Are The Types Of Screw Points?
1. Type A: This threaded screw made for using thin metal, typically between .015 to .050, that makes these screws idea for drilled, punch, or nested holes in sheet metal that reside in plywood, asbestos combinations, and various other materials. Type A screw points are not recommended for new designs.
2. Type AB: AB screw points combine the locating point of Type A with the thread size and pitch of Type B.
3. Type B: B screw points are typically used in heavier metals around .050 to.200 thick with larger root diameter and fiber thread. The finer thread allows for light and heavy sheet for non-ferrous metal casting, plastics, and asbestos combinations.
4. Type 1 point: Known as a cutting screw with a single flute for general use that products a fine machine screw thread for field replacements.
5. Type 17: Typically used for wood with a coarse tapping screw thread with a long sharp point fluted to capture chips.
6. Type 23: This thread cutting screw offers maximum thread cutting area with an optimal chip clearing and minimum tightening torques.
7. Type 25: Similar to type 23 but offers a coarse Type B thread for plastics and other softer materials. Its design includes a large chip clearing and cutting edges.
8. Type F: Equipped with a machine screw thread with a blunt tapered point and multi-cutting edges along with chip cavities. These screws can be used for heavy gauges sheet metals, such as aluminum, zinc, lead die castings, cast iron, brass, and plastics.