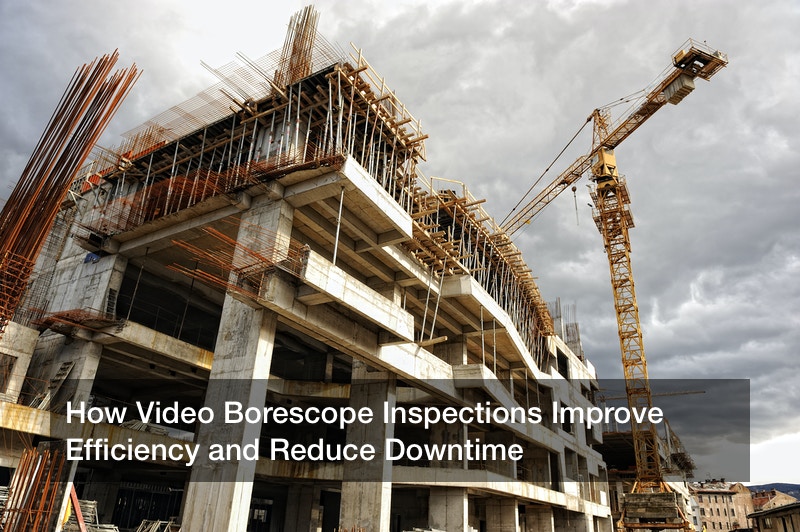
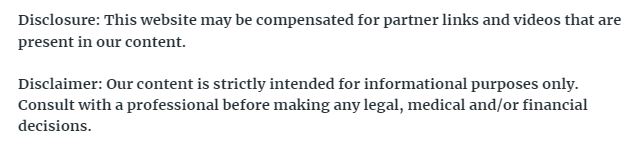
Regular borescope inspections are crucial for the proper working of steam and gas turbines. Turbines operate in severe industrial conditions where the temperature can exceed one thousand Fahrenheit. They require periodic maintenance to uphold their mechanical integrity.
Therefore, there is a need for a cost-effective way to address these challenges without exposing the plant to significant downtime. In recent years, borescope inspection services have adopted advanced technology. Different types of devices have varying solutions for a wide range of industrial applications. In this article, we’ll look at some of the benefits of the borescope for gas turbine inspections.
Detecting Obstructions and Dirt
If you are running a plant, the last thing you need is a machine that breaks down unexpectedly. You can prevent downtimes by strictly following maintenance routines. For the turbine inspection to be effective, the testing equipment ought to have the capacity to capture the relevant details.
If dirt gets into the combustor of gas turbines, it can cause a temperature differential in the unit. Oil, moisture, sand, and other types of debris may go past the filter. Different types of obstructions may accumulate and eventually cause the system to fatigue.
One advantage of inspecting turbines with a borescope is that the device allows for quick inspections. Modern devices can project images with full HD resolutions. As a result, finding the fault is much faster because the details are easy to discern without dismantling critical parts of the machinery.
Minimize Future Damage
Gas turbines need to be monitored closely to catch damages before they become problematic. For example, hot corrosion is triggered by oxidation that takes place at considerably high temperatures. The machine can generate temperatures of more than 500 degrees centigrade.
Hot corrosion is known to cause damage to the turbine in areas subjected to severe stress. Minerals and metallic parts can react during oxidation. As a result, certain parts of the turbine, such as the base of the blade, may become prone to cracking and breakage.
Turbine inspections can help pinpoint areas where oxidation may be weakening the system. There may be places where bolts will need to be tightened. It may be necessary for technicians to know exactly where the problem has occurred for effective parts retrieval.
Minimize Downtime
Boroscopic inspection of a gas turbine does not leave a lot of room for errors in fault detection. It generates high-resolution images that are projected on an electronic screen. It allows technicians to work in the plant to diagnose the issue properly.
For example, if you detect cracks, your technician may be in a better position to understand its course. The cracks may be from stresses the machine is subjected to or it as a result of oxidation and fatigue.
With quality images, the plant can prescribe an effective remedy for the problem. If the issue is oxidation, the technicians may change the water and check for the presence of contaminants. You can use high-resolution images and videos to visualize the progression of the problem and how it may evolve in the future.
Objective Management and Timely Assessment
Other types of turbine inspections are not as specific as the video borescope evaluations. The data is specific, which allows for the condition-based maintenance of the machinery. Precise information ensures guesswork is eliminated from the process.
Additionally, the process of inspection and maintenance is timely. The plant can detect faults with the turbine at the earliest stages to prevent complications and downtime. The accuracy of the visuals enables the technician to understand the nature of the fault before it can manifest into an inefficiency.
In Conclusion
All in all, advanced borescope inspections can make cleaning of the equipment more precise, and parts removal less complex. They are reliable, accurate, and simple to use for maintenance and repair tasks. They can improve the longevity of the gas turbines and boost the plant’s bottom line. If you have any questions about turbine inspections, do not hesitate to contact us today.