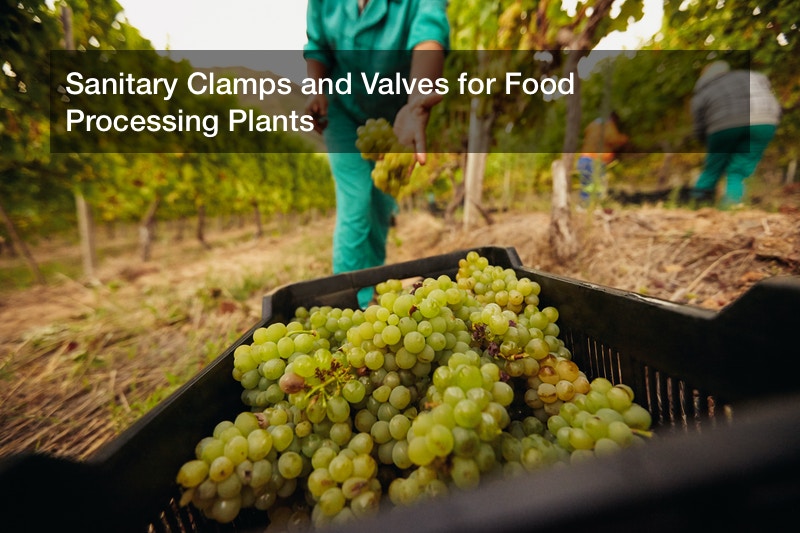
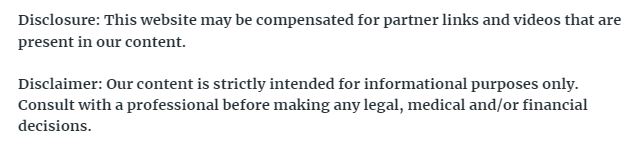
Many industries need pipes, tanks, valves, clamps, and pumps to transfer and process fluids during everyday work, and these fluids range from crude oil and pharmaceutical chemicals all the way to edibles such as milk, water, and soft drinks. In the latter case, such as milk processing plants, it is important to use sanitary clamps, sanitary pipe valves, and sanitary welding, among other hardware, to avoid contaminating the fluids. These sanitary valves and sanitary clamps are often made of stainless steel and need to be cleaned regularly, though some pumps that work with thin liquids can even be made of plastic. What is there to know about the installation, use, and cleaning of these sanitary clamps and valves in a processing plant?
Steel Clamps and Valves
Many of these processing plants feature countless clamps, pipes, and valves made of steel, often Stainless Steel 304 in particular. In fact, food and pharmaceutical processing ranks in the top five most common uses of Stainless Steel 316, and stainless steel comes in around 100 grades overall. These steel grades are tough but lightweight compared to iron, and they resist corrosion and rust (hence the name), vital for work when exposed to fluids and chemicals all day long. It is believed that under typical work conditions, stainless steel pipes can last around 100 years, and the crews at a milk processing plant have every reason to keep their sanitary clamps and valves clean and in good working order.
In a milk processing plant, for example, sanitary check valves are put in place to regulate how milk can move from different pipes and tanks, and the valves will not allow unsuitable materials to get deeper into the system (hence they are “check” valves). The milk must have certain qualities to be deemed safe to consume, and any unprepared milk is blocked via these valves and is sent back to earlier tanks for more processing. Prepared milk, by contrast, will pass through the valves just fine. Meanwhile, what about the sanitary clamps?
Take note that the pipes used in milk processing plants must be frequently taken apart for cleaning, so it is most practical to hold them together via leak-free sanitary clamps rather than riveting or screwing them together. Of course, this means that the stainless steel sanitary clamps must be engineered to endure constant pressure and heat during work, without allowing any leaks or ruptures to occur. What is more, these sanitary clamps must also meet FDA sanitary standards, to help prevent the unsafe buildup of bacteria or other harmful elements in the hardware.
How do clamps stay sealed while working? Often, they make use of one or more bolts that can be tightened, and two-bolt models are often the most secure of all. Such clamps are put in place, then tightened to the right pressure for work, and can be loosened again for easy removal. Still, while efficient and tough, these sanitary clamps are going to need routine cleaning and inspections so problems can be diagnosed early on. Such clamps are resistant to corrosion due to their steel grades, but old, well-worn clamps may start to develop unsafe corrosion, and they must be replaced once found. Also, it is not unthinkable for clamps to pop loose if the pipe’s pressure climbs too high, such as if there was a malfunction with the system. Strained or damaged clamps must be found and replaced right away, or repaired if possible. A milk processing plant’s manager should know which wholesale suppliers to consult for the quick shipment of new parts.
Even if no leaks or corrosion takes place, routine cleaning is a must. After operations are shut down, the plant’s pipes, valves, and clamps are thoroughly rinsed with water, and broken apart from each other for thorough cleaning and inspections. It is vital that no milk residue is allowed to remain in the pipes or valves and harden, thus attracting harmful bacteria. Strict FDA guidelines are in place, to determine what constitutes properly clean valves, clamps, and pipes in a processing plant, and any new personnel should get thorough training and learn those standards quickly.