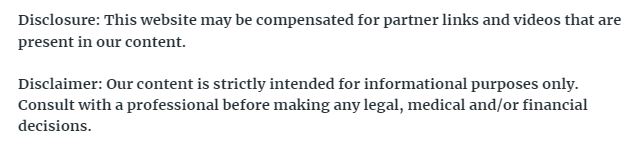

Finding the right metal is perhaps the most important part of the manufacturing process. You can locate skilled craftsman to weld and experienced marketers to reach out to customers, but all of that work can be easily undone if your materials aren’t up to snuff. The molybdenum manufacturing process is being chosen over other resources for its more thorough approach to a classic method. When four major mineral forms are combined with calcium or iron, countless industries are offered the chance to benefit from a material that can stand up to incredible heats and retain density even under astounding pressure.
The name of the game these days is a material that isn’t just durable, but environmentally friendly and able to save manufacturers plenty of money down the road. Stainless steel and aluminum have been popular for decades for their combination of efficiency and accessibility, with an estimated 80% of both regularly recycled and reused every year. They’re not the only ones on the market, however, and the molybdenum manufacturing process is starting to grow in popularity once more. Customers want a product that will last, after all, and you can provide that to them by choosing right the first time.
A few centuries back the appeal of molybdenum manufacturing methods gained traction among separate sectors. It was recognized as an official element in the late 1700’s and has since been used for a wide variety of purposes. Tungsten was discovered later that same century, though it still wouldn’t be actively applied to any one industry for another 150 years. Due to its incredible density and durability under heat it’s starting to be sought out by manufacturers keen on standing out from the competition. Vacuum furnaces and vacuum parts are especially popular here.
Just how durable are tungsten and molybdenum materials? For starters, tungsten is more than twice as dense as steel and has the highest melting point of all metals in its purest form — as much as 6,170 degrees Fahrenheit alongside a high tensile strength and low vapor pressure. Some estimates have seen tungsten boasting a tensile strength of 1,510 megapascals and falling between an 8.5 and 9 on the Moh’s hardness scale. Tungsten alloy machining embraces the unique qualities of tungsten and applies them in mining excursions, metalworking and various scientific industries.
With tungsten just a notch below diamonds in hardness and easily one of the most preferable choices for most automotive and manufacturing industries, it can be easy to overlook the molybdenum manufacturing process. Molybdenum has a very high melting point of 4,748 degrees Fahrenheit — vacuum furnaces are capable of reaching temperatures well above 1,200 degrees Celsius (or 2,192 degrees Fahrenheit), which means anything less risks eroding or melting right under the customer’s nose. Medical, electronics and crystal growth all benefit from the incredible properties of molybdenum and tungsten.
Miners have estimated there only being 1.25 grams of tungsten for every 1,000 kilograms of the Earth’s crust. With more businesses appreciating the results of molybdenum and tungsten, you’ll want to hurry up and stake your claim quick. What can a moly threaded rod do to make your brand stand out?