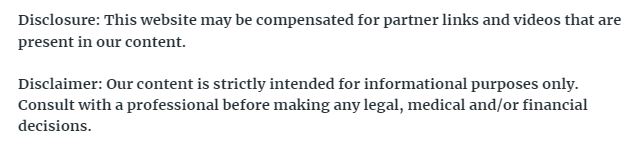
From in-plant modular offices to modular homes to warehouse partitioning systems, modular construction methods can be put to many good uses here in the United States. After all, modular construction is on the rise, with more than 90% of engineers having used it at least once – and more than 80% of contractors having used it as well. Even very nearly three quarters of all architects have become to dabble in methods of modular construction as opposed to traditional methods of construction.
In part, modular construction has gotten so popular simply because it is so applicable and so useful for many different structures and types of buildings all throughout the country and even in many places abroad as well. In-plant modular offices represent one application of modular construction methods, but these in-plant modular offices are far from the only structures that modular construction methods can be used to build. Modular homes, for instance, have also risen in popularity, providing relatively low cost living for many people throughout the United States, people who might not otherwise have ever been able to afford a home.
In addition to these very lucrative and promising applications of modular construction, about half (around 49%, to be more exact) of all modular construction endeavors actually go towards the building of healthcare facilities. Another 42% or so of modular facilities are dorm buildings and other types of student housing. In addition to both of these applications for modular construction, another 42% of all modular construction projects revolve around the construction of various manufacturing facilities all throughout the country.
But why, exactly, are modular construction methods so ideal for everything from the construction of hospitals and dorms to the construction of in-plant modular offices? For one thing, modular construction methods are far less expensive than the traditional construction methods that are so commonly used for construction projects both big and small. In fact, the data that has been gathered on the subject more than backs up this claim, showing that construction costs can be reduced by a hugely impressive 20% when modular methods of construction are used for buildings like in-plant modular offices, among many other. And while 20% of the money spent might not always be saved, savings through the use of modular construction typically do not dip any lower than 9% at the very least.
In addition to this, modular buildings can typically be built much more quickly than buildings that are built through the use of traditional construction methods, which can often take up to six months – if not even longer – to fully and thoroughly complete. Modular construction methods, on the other hand, often take only a few weeks, primarily due to the fact that the bulk of any modular construction project is typically completed in a factory setting instead of actually on the site. In fact, one man in China devised a 57 story building that was constructed in a mere 19 days – just over two weeks. Without modular construction methods, this truly impressive feat would have likely not been possible.
Modular construction methods, such as those seen used for in-plant modular offices, are also ideal from an environmental standpoint as well. As many people know, simply from walking by one even, traditional construction sites often produce so much total waste that, by the time that the construction project has been completed, dumpsters are needed to haul all of the trash away. And while some of it, such as the wood waste, might be recycled, this is not a given. And even if it is, not all of it will be able to be recycled anyway.
But modular construction, thankfully, is a much different story. In fact, modular construction reduces the waste materials produced at the typical construction site using traditional methods by as much as 90%. This is due to the fact that many of the traditional materials you’d see at such a location, ranging from cement, timber, and concrete (among many others), simply are not used in the same capacity.