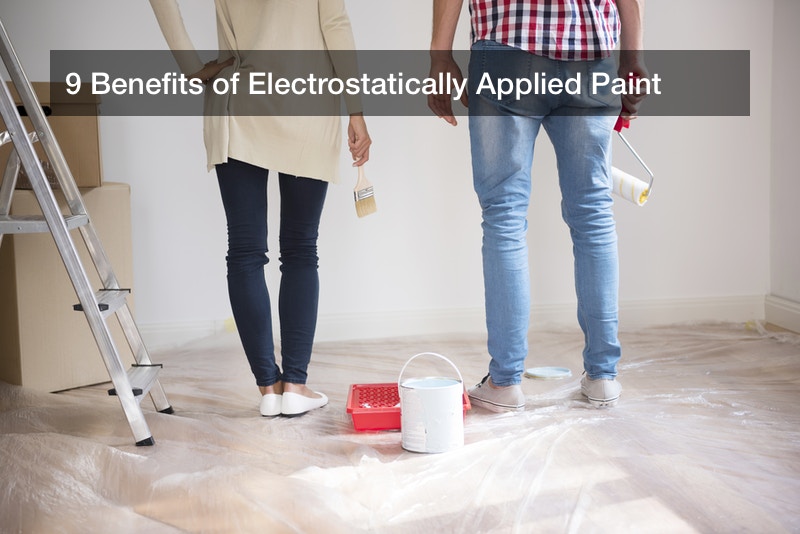
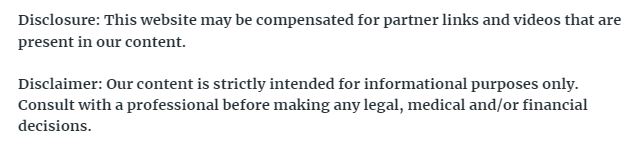
The use of powdered coatings in the manufacturing sector is on the rise. It mainly stems from the fact that professional finishes are essential for industrial metal products.
Approximately 10% of the total industrial finishing applications in the US now use this technology. To help you understand why here are nine benefits of electrostatically applied paint .
1. Durable
The process of putting a professional powder coating involves using an electrostatic gun to apply a thick coat of dry powder that is then set in an oven to cure. The result is a thick, dense coat that is resistant to scratching, flaking, or fading. The products have a higher resistance to chipping and abrasion. The protective coating will keep the colors bright and vibrant for longer.
2. Corrosion Resistance
Rusting is a common problem that plagues most industrial fabricated metal products. The metals are exposed to corrosive environmental elements and chemicals. Powdered surfaces are evenly coated with a thick layer that protects the metal from rust.
3. Diverse Range of Products
The powder coating industry has grown in leaps and bounds, with manufacturers finding new ways to apply the dry powder on different materials. Therefore, regardless of the shape, size, and conformity of your industrial products, they can still be coated using this technique.
4. Color Variety
Dry powders come in a variety of hues and shades that can be easily customized for unique blend finishes. You can choose from an infinite range of colors such as glossy, fluorescent, glitter, high-gloss, and clear. The colors blend perfectly in the curating oven creating a professional finish.
5. Cost-Effective
Powder coatings do not require additional solvents such as thinners, thus making them cheaper. You require fewer raw materials that can be purchased in size, avoiding wastage. The processing time needed for the paint to dry and cure is shorter than in wet painting. It saves not only time but also energy costs.
6. Appearance
Powdered metal products have a smooth and uniform layer that is pleasing to the eye. The dry powder melts and coats evenly on the surface of the metal. Powder coating is cleaner, smoother, and with a more superior finish compared to liquid paint jobs.
7. Eco-friendly products
Paints usually require the addition of various solvents that contain Volatile Organic Compounds (VOCs.) Dry powders do not contain the VOCs, making them friendlier to the environment. You don’t need to enforce strict pollution control measures to remain compliant with Environmental Protection Agency Rules.
8. Less Waste Product
Over spray is a common occurrence when applying liquid coatings and it contributes to a lot of wastage. The electrostatic spraying ensures virtually every dry powder particle sticks to the metal surface due to the difference in charges. You can collect any residual powder from overcoats and reuse it, thus reducing the waste produced.
9. Maintenance
Powdered metal surfaces are easier to maintain than painted ones. The powder forms a thick layer that is resistant to scratching and corrosion. No special solvents or chemical cleaners required to remove dirt from the surface. You would have to worry about damaging the product from the cleaning process.
Bottom-Line
Powder coating is an excellent choice when it comes to achieving a professional finish for your products. You can create uniformity in your products and a custom blend from the variety of hues available. It’s no surprise why powered coating has taken over the finishing industry by a storm.