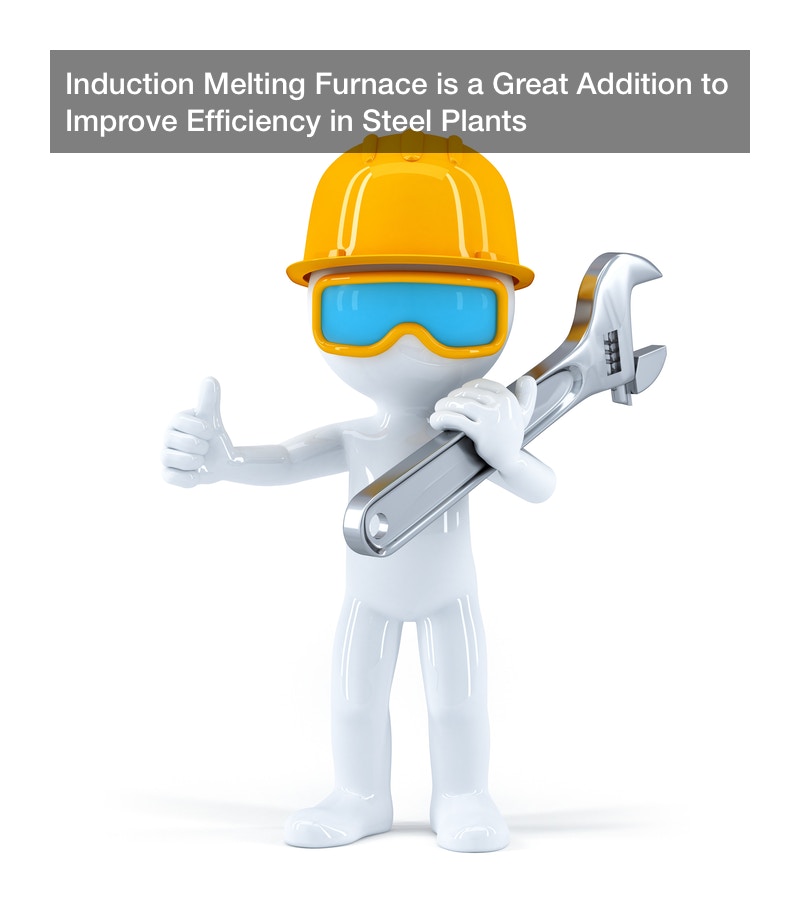
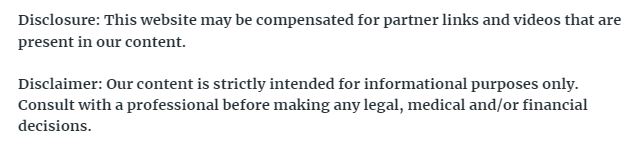
Steel melting induction furnace is used for forging and casting stainless steel and other ferrous and non-ferrous metals such as iron, brass, gold, bronze, aluminum alloys and copper.
Induction furnaces have varying power range and melting capacity and some are designed to be utilized in low to high power density, producing high-quality steel casting. This equipment is commonly employed in foundries, metal casting shops or factories that make machines.
Induction Melting Furnace Components and Configuration
Induction melting furnaces comprise essentially a single unit — made of two fabricated casings and other components including hydraulic cylinders, that serves as the melting chamber. Sheet-rolling stainless steel is used as well as induction coils — water-cooled copper conductors, and electric power which are all fitted inside the unit.
To achieve an ideal induction furnace inclination, which is at 95 degrees, the hydraulic rams can be adjusted properly with the help of a supervisory control station.
Steel melting induction furnaces typically run on three-phases switching a 3 phase power and 380 volts from individual converter using a semiconductor device, commonly known as a thyristor frequency converter — which is a device that converts the three-phase current to single phase industrial power frequency.
A complete induction furnace has an in-built control panel that allows the monitoring and control of the converter. Automatic frequency control is also within the system allows proper heat transfer to the load for improved casting efficiency.
Another key component in a steel melting induction furnace is the water cooling unit, which forms an important part of the entire system. A cooling system host the control and signaling sensors that keep all the functions of a furnace operating optimally.
The furnace configuration and all the components are designed to offer efficient heating equipment with numerous benefits. Some of the benefits of induction furnaces include:
- Reliable converters
- High melting capacity and power
- Optimized parts
- Energy efficient
- Higher efficiency coefficient
High Production Rate and Low Fuel Consumption
The increased need for efficiency in the metal casting industry is seeing the introduction of quality induction furnaces that delivers excellent results. Induction furnaces have made the metal production much easier because they can be built for both small scale and large scale production.
Unlike traditional furnaces, which are mostly limited to melting small quantity of metal because of their size, induction furnaces can evenly cast large quantities of metals with a minimum loss, regardless of the furnace size. For a metal production company, this is a great asset for scaling up production effectively without the need for further machine acquisition or additional investment.
Control and Optimization of the Melting Process
One element that makes steel melting induction furnace so effective is the ability to control and optimize the melting process. The melting temperatures can be controlled. Best yet, an induction furnace can be used to melt different types of metals, provided the temperature is controlled accordingly because they all have different melting points.
In addition to the control of temperatures, other things can also contribute to the melting process. Electrical coils, in particular, are known to affect the process due to the generation of extra magnetic force fields. This is based on the scientific interaction between the magnetic fields produced by the coil and the temperature gradient.
Reduced Cost of Operating
The efficiency brought about by induction furnaces translates to huge savings for steel plants that have employed this system. Regular furnaces are energy-intensive and reaching high-temperature means more on your power bill.
However, an electric-powered induction furnace requires less energy to melt metal and it can evenly apply intense heat to casting metal with minimum energy loss.
The induction furnace and steel production industry have seen immense advancement in technology, which is why it can be regarded as the fastest growing industry. Given that most of the raw material used to make furnaces are recycled, this ensures the sustainability of steel and metals, in general.