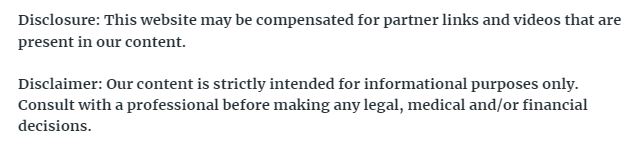
Within trade school class offerings and blue-collar jobs one popular and always in-demand option for those looking for a good career is welding services. Most professional welders go to specialized training and classes to learn about welding and get a foundation with the basics of welding, the types of welding commonly done, and how it can translate to a profitable career.
After learning all about welding and with a good foundation of education, training, and hands-on experience, welders can enjoy a varied and successful career. There are many industries and niche markets to get into as a welder. Each focus will require slightly different tools, training, and processes and some are more in demand and profitable than others. A lot depends on current market trends, how many welders in the area are offering particular services, and how the overall economy is holding up.
The good news is that when it comes to American welding services there is almost always a decent demand as welding can be utilized in many markets and there are many ways welders can impact residential and commercial construction and maintenance.

Without welding, where would we be?
Many of the products we know and love today would simply not be possible. Thanks to modern technology increasing at an exponential rate we can expect even better quality products in half the time, with steel fabrication and welding equipment bridging the gap between experienced artisans and new students alike. Should you be considering the field of welding to address any of your problems, from repair to a new career field, you’ll find yourself in good hands. Today’s manufacturing company is more than prepared to address any issues head-on.
Learn more about steel fabrication, machinery repair and the origin of this irreplaceable form of construction.
It’s estimated more than 50% of all products made in the country require welding at some point in time. What kind of products? Items as small as a printed circuit board and as large as an eco-friendly car all need some form of welding to make sure they hold up to wear and tear. Not all welding is made the same, however. Just like any other industry, welding offers different specialties to better address all sorts of demands. Conveyor belt repair, dryer repair and food and beverage manufacturing are just a few of the areas that rely on welding to see fruition.
TIG welding, for starters, was developed back in the 1930’s. Today you can find this technique used in aerospace, automotive repair and various art fields, such as sculpture or set design. Short for ‘Tungsten Inert Gas’, this form of welding is unique for relying heavily on a non-consumable tungsten material to provide a solid end result. The most common metals used for TIG welding are copper and titanium. MIG welding would later be developed in the 1940’s and is considered a much faster and more reliable welding system than stick welding.

Believe it or not, welding is not a new technique. In fact, the earliest known record of welding occurred all the way back in 3,500 B.C. Gold, copper, bronze, iron and silver were melted and joined together with more crude methods to create tools, jewelry and weapons. The biggest difference is today’s welding is considerably more advanced and readily available, with manufacturing companies and hobbyists alike turning to it to see all sorts of projects see the light of day. Steel fabrication has also seen more metals than ever provided on a wider level, creating some of the quickest and highest quality products of the century.
Aluminum, in particular, is one of the most recycled materials on the planet. A recent estimate has seen 75% of all aluminum produced in the United States still being in use today. Another commonly used material is stainless steel, dubbed such for its ability to hold up well to temperature, moisture and the elements without rusting or degrading. No processing plant is complete without these basic metals. With the world becoming increasingly eco-conscious, being able to recycle and reuse is often the gamechanger.
Thanks to this consistent demand you won’t go wrong applying for a full-time job in welding. By the time 2020 arrives the international metal fabrication equipment market is going to see a growth surge of 8%. Fabricated metals are also the third largest American manufacturing industry when measured by employment alone. Welding companies are always on the lookout for passionate and invested craftsman eager to leave their mark on fields ranging from automotive to art. Brazers, cutters and solderers are going to reach an impressive 450,000 by 2024.
Whether you’re a processing plant in need of a quality boost or someone looking for a reliable career field, the art of welding is here to stay.
