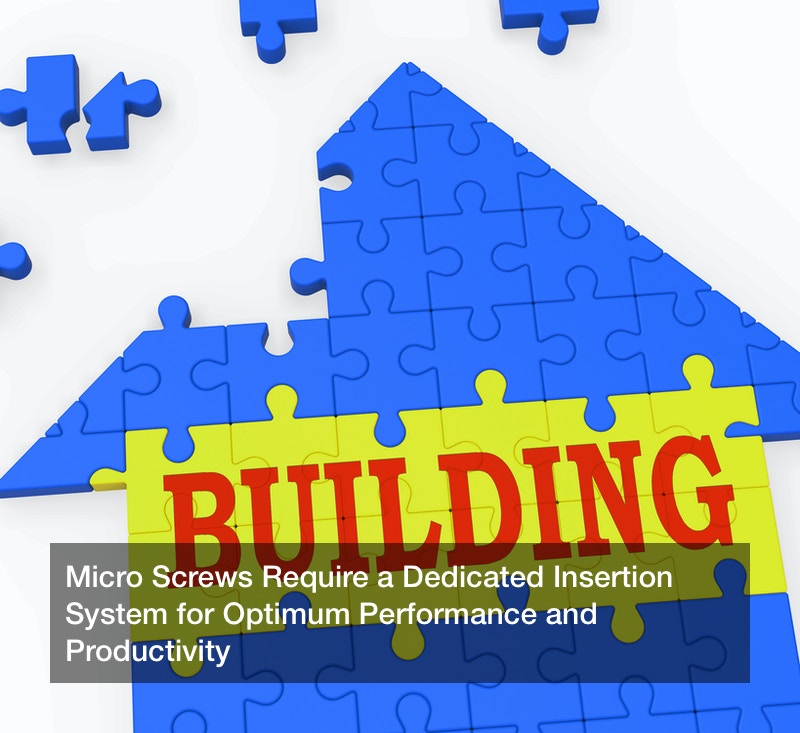
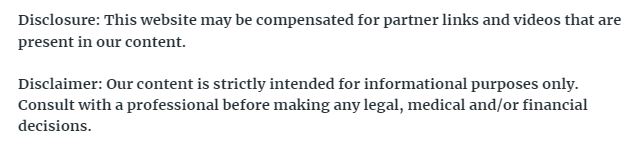
If you’ve dealt with screws before while working with different tools, you’ve probably accustomed to the standard sizes that hold electronics and appliances. However, screws are available in different sizes from those big ones utilized to assemble detailed parts of a plane to small screws securing smartwatches and other small gadgets. Regardless of the size, most of the things we depend on today are held together by multiple screws.
The concept of the screw dates back to around 200 B.C., and since then it has become an integral part of human production. Early screws had to be handmade, so no two were ever alike and not of quality due to subpar materials. The process was also time-consuming and nearly impossible for mass production. In 1928, the National Screw Thread Commission established a standard for screw threads for interchangeability. Today, machining of screws and thread rolling has opened up a plethora of custom screw options and they’re not identical simply because of their specific use.
Originally, screws were grooved in shape, but with improved technology and increased specialization, they’ve completely evolved from basic screws — slotted drives and Phillips to screw head options such as square drives, cruciform drives, square socket, internal hex drives, just to mention a few.
The different types of screw heads are used with and for different purposes. For instance, the basic Phillips and slotted screw heads are commonly used for furniture and cabinetry but ideal to use with an electric screwdriver. These two are perhaps the most commonly used types of screws in the U.S., and they can be found in possibly any furniture and cabinet in your house from kitchen cabinets to bathroom vanities.
The main categories of screws are metal, wood, and drywall screws, but the list includes also other specialized screws like micro metal thread forming screws, microplastic forming screws, screws with captive washer (SEMS), and dual lead thread forming screws (Hi-Lo screws), which are highly used in industrial applications. As the world keeps figuring out diverse applications of screws, we can expect to see advanced systems in the near future.
Screws are available in different lengths, thread size and material including steel, aluminum, brass, and other different metal alloys. Custom fastener options are also available in different styles such as case hardened, oxidized or plated screws. When you’re choosing screws for your project — whether securing electric component, fastening cabinets and furniture, you need to first define the parameters of the screws you’re looking for; this is in addition to the size, material and type. Other things to consider include the type of coating — thread locking or lubrication, and torque requirements of a screw which could range from low to high depending on the material used.
When choosing your screw options another important thing to consider is the insertion method. Big and medium screws are much easier to insert using both manual and special fastening tools. Small screws, however, have traditionally been a problem when inserting and is associated with a number of occupational issue such as high cost of production and reduced productivity. Traditional insertion methods also don’t guarantee proper seating torque particularly for small screws, and this could cause them to loosen compromising the integrity and safety of the secured item.
The screw, nut, and bolt industry continues to grow as it adopts better production methods for improved performance and safety. This drive has led to more advanced systems with minimum production costs that support the dynamic environment in improving fastener options in the market.