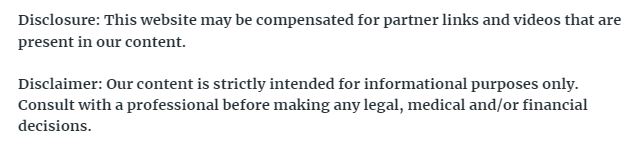

Prefabrication and modular construction processes are becoming more common. This is because they save energy, time, materials, and costs. Furthermore, since modular construction can be either permanent or mobile, this is another welcome benefit. While some projects may be completed in their entirety using these methods, others may employ these processes to modify existing spaces.
Types of Prefabricated and Modular Constructions
A recent survey found that roughly 90% of the engineers that responded indicated they used these processes on some of their projects. Contractors and architects also used these methods on some projects, with 84% of the former and 76% of the latter indicating that they did so.
Another survey found that prefabricated and modular construction was popular for a variety of construction purposes and projects during 2011. This included the following commercial applications:
- Healthcare facilities: 49%
- Dormitories and other college buildings: 42%
- Manufacturing facilities: 42%
When entire structures don’t need to be made, prefabricated office walls or warehouse partitioning systems can be constructed within existing structures to modify those spaces. Portable office walls and partitions are also an option when different spatial configurations are needed to accommodate specific projects, personnel, or storage.
The Benefits of Prefabricated and Modular Construction
About 60% to 90% of prefabricated construction is handled in a warehouse or factory setting. As a result of being in a controlled environment, projects can be completed in a shorter period of time. It’s important to note that quality is still maintained when modular methods are used.
Energy consumption is also greatly reduced during the modular construction process. Recent data shows that this can be as much as 67%. After being completed, there will be further savings to the occupants, which is due to the end product’s energy-efficient features.
Overall construction costs could also be reduced when more buildings and spaces are constructed using modular methods. The Building Industry Association of Philadelphia issued a report that showed these savings could range from nine percent to 20%. In addition to the time and energy-saving factors, these savings are increased because fewer traditional building materials are needed or wasted.
The Waste and Resources Action Programme, which is based in the United Kingdom, reported that waste could be reduced by as much as 90% with modeular construction methods. Since the need for materials such as cement, bricks, timber, concrete, wood pallets, shrink wrap, cardboard, and plasterboard will be reduced to this extent, it can make a significant impact.
Learn More About Modular Construction
If you have a large building that needs to be modified or restructured, prefabricated office walls or partitions may be the best solution. In addition to having prefabricated office walls installed, you may want to consider having a prefab office space delivered to your site. When you speak with a representative about the type of structure that is needed, you will be able to learn more about the benefits of going modular.